Vahvlite tükeldamise tehnoloogia kui pooljuhtide tootmisprotsessi kriitiline samm on otseselt seotud kiibi jõudluse, saagikuse ja tootmiskuludega.
#01 Vahvlikuubikuteks lõikamise taust ja tähtsus
1.1 Vahvli tükeldamise definitsioon
Kiipide tükeldamine (tuntud ka kui kritseldamine) on pooljuhtide tootmise oluline samm, mille eesmärk on jagada töödeldud kiibid mitmeks eraldi kiibiks. Need kiibid sisaldavad tavaliselt täielikku vooluringi funktsionaalsust ja on elektroonikaseadmete tootmisel lõpuks kasutatavad põhikomponendid. Kuna kiibi konstruktsioonid muutuvad keerukamaks ja mõõtmed pidevalt vähenevad, muutuvad kiipide tükeldamise tehnoloogia täpsus- ja efektiivsusnõuded üha rangemaks.
Praktikas kasutatakse vahvlite tükeldamiseks tavaliselt ülitäpseid tööriistu, näiteks teemantkettaid, et tagada iga stantsi terviklikkus ja täielik funktsionaalsus. Peamised etapid hõlmavad ettevalmistust enne lõikamist, täpset kontrolli lõikamisprotsessi ajal ja kvaliteedikontrolli pärast lõikamist.
Enne lõikamist tuleb kiip märgistada ja positsioneerida, et tagada täpsed lõiketeed. Lõikamise ajal tuleb kiibi kahjustamise vältimiseks rangelt kontrollida selliseid parameetreid nagu tööriista rõhk ja kiirus. Pärast lõikamist viiakse läbi põhjalikud kvaliteedikontrollid, et tagada iga kiibi vastavus jõudlusstandarditele.
Kiipide tükeldamistehnoloogia põhiprintsiibid hõlmavad lisaks lõikeseadmete valikule ja protsessiparameetrite seadmisele ka materjalide mehaaniliste omaduste ja karakteristikute mõju lõikekvaliteedile. Näiteks on madala k-sisaldusega dielektrilised räniplaadid oma halvemate mehaaniliste omaduste tõttu lõikamise ajal väga vastuvõtlikud pingekontsentratsioonile, mis põhjustab rikkeid, nagu mõrasid ja pragunemist. Madala k-sisaldusega materjalide madal kõvadus ja rabedus muudavad need mehaanilise jõu või termilise pinge all, eriti lõikamise ajal, vastuvõtlikumaks struktuurilistele kahjustustele. Tööriista ja kiibi pinna kokkupuude koos kõrgete temperatuuridega võib pingekontsentratsiooni veelgi süvendada.
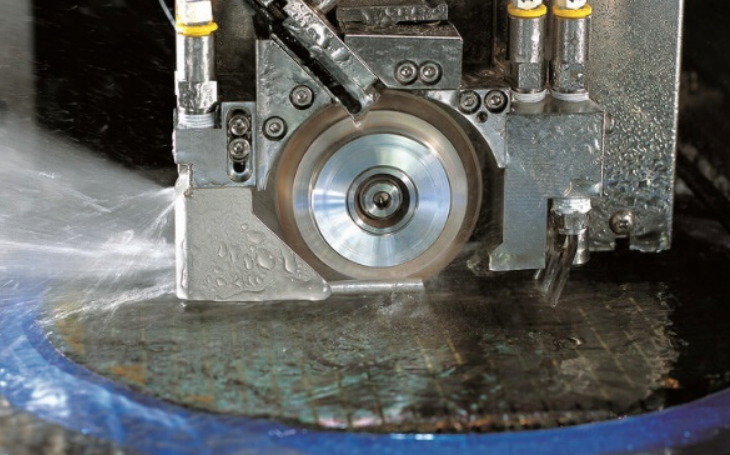
Materjaliteaduse edusammudega on vahvlite tükeldamistehnoloogia laienenud traditsioonilistest ränipõhistest pooljuhtidest kaugemale, hõlmates uusi materjale nagu galliumnitriid (GaN). Need uued materjalid esitavad oma kõvaduse ja struktuuriliste omaduste tõttu tükeldamisprotsessidele uusi väljakutseid, mis nõuavad lõikeriistade ja -tehnikate edasist täiustamist.
Pooljuhtide tööstuses kriitilise protsessina optimeeritakse vahvlite tükeldamist jätkuvalt vastavalt muutuvatele nõudmistele ja tehnoloogilistele edusammudele, pannes aluse tulevastele mikroelektroonika ja integraallülituste tehnoloogiatele.
Kiipide tükeldamistehnoloogia täiustused ulatuvad kaugemale abimaterjalide ja tööriistade väljatöötamisest. Need hõlmavad ka protsesside optimeerimist, seadmete jõudluse parandamist ja tükeldamisparameetrite täpset juhtimist. Nende edusammude eesmärk on tagada kiipide tükeldamisprotsessis suur täpsus, tõhusus ja stabiilsus, rahuldades pooljuhtide tööstuse vajadusi väiksemate mõõtmete, suurema integreerituse ja keerukamate kiibistruktuuride järele.
parendusala | Konkreetsed meetmed | Efektid |
Protsesside optimeerimine | - Parandada esialgseid ettevalmistusi, näiteks täpsemat kiipide positsioneerimist ja teekonna planeerimist. | - Vähendab lõikevigu ja parandab stabiilsust. |
- Minimeerib lõikevigu ja parandab stabiilsust. | - Tööriista rõhu, kiiruse ja temperatuuri reguleerimiseks võtke kasutusele reaalajas jälgimis- ja tagasisidemehhanismid. | |
- Madalam kiibi purunemismäär ja parem kiibi kvaliteet. | ||
Seadmete jõudluse parandamine | - Kasutage ülitäpseid mehaanilisi süsteeme ja täiustatud automatiseerimisjuhtimistehnoloogiat. | - Suurendage lõiketäpsust ja vähendage materjali raiskamist. |
- Tutvustada laserlõikustehnoloogiat, mis sobib suure kõvadusega materjalidest vahvlite jaoks. | - Parandada tootmise efektiivsust ja vähendada käsitsi tehtud vigu. | |
- Suurendage seadmete automatiseerimist automaatseks jälgimiseks ja reguleerimiseks. | ||
Täpne parameetrite kontroll | - Reguleerige parameetreid, nagu lõikesügavus, kiirus, tööriista tüüp ja jahutusmeetodid, täpselt. | - Tagage matriitsi terviklikkus ja elektriline jõudlus. |
- Kohanda parameetreid vastavalt vahvli materjalile, paksusele ja struktuurile. | - Suurendage saagikust, vähendage materjalijäätmeid ja alandage tootmiskulusid. | |
Strateegiline tähtsus | - Pidevalt uurida uusi tehnoloogilisi teid, optimeerida protsesse ja täiustada seadmete võimekust, et rahuldada turu nõudlust. | - Parandada kiibitootmise saagikust ja jõudlust, toetades uute materjalide ja täiustatud kiibidisainide väljatöötamist. |
1.2 Vahvlikuubikuteks lõikamise olulisus
Kiipplaatide tükeldamine mängib pooljuhtide tootmisprotsessis kriitilist rolli, mõjutades otseselt järgnevaid etappe ning lõpptoote kvaliteeti ja jõudlust. Selle olulisust saab üksikasjalikult kirjeldada järgmiselt:
Esiteks on tükeldamise täpsus ja järjepidevus kiibi saagikuse ja töökindluse tagamisel võtmetähtsusega. Tootmise käigus läbivad vahvlid mitu töötlemisetappi, moodustades arvukalt keerulisi vooluringistruktuure, mis tuleb täpselt jagada üksikuteks kiipideks (stantsideks). Kui tükeldamise käigus esineb olulisi joondamis- või lõikamisvigu, võivad vooluringid kahjustuda, mis mõjutab kiibi funktsionaalsust ja töökindlust. Seetõttu tagab ülitäpne tükeldamistehnoloogia mitte ainult iga kiibi terviklikkuse, vaid hoiab ära ka sisemiste vooluringide kahjustumise, parandades üldist saagikust.
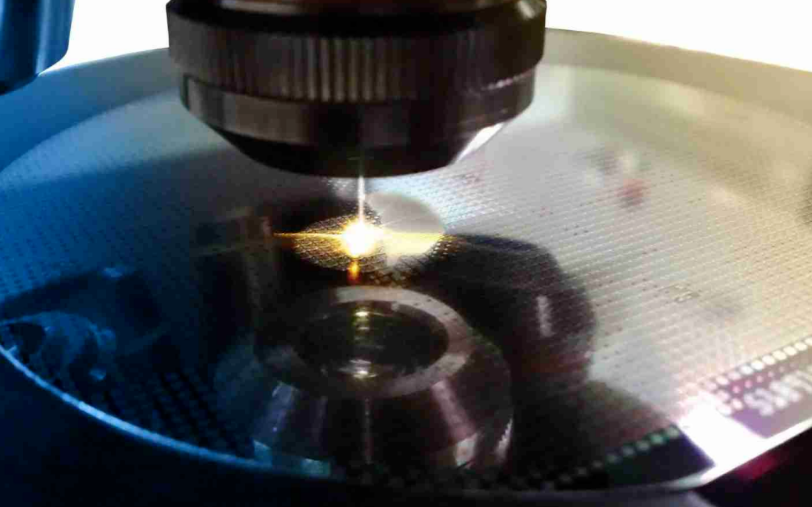
Teiseks, vahvlite tükeldamine mõjutab oluliselt tootmise efektiivsust ja kulude kontrolli. Tootmisprotsessi olulise etapina mõjutab selle efektiivsus otseselt järgnevate etappide edenemist. Tükeldamisprotsessi optimeerimise, automatiseerimise taseme tõstmise ja lõikekiiruse parandamise abil saab üldist tootmise efektiivsust oluliselt parandada.
Teisest küljest on materjali raiskamine tükeldamise ajal kulude haldamisel kriitilise tähtsusega tegur. Täiustatud tükeldamistehnoloogiate kasutamine mitte ainult ei vähenda ebavajalikke materjalikadusid lõikamisprotsessi ajal, vaid suurendab ka kiipide kasutusastet, vähendades seeläbi tootmiskulusid.
Pooljuhtide tehnoloogia arenguga suurenevad kiipide läbimõõdud pidevalt ja vastavalt ka vooluringide tihedus, mis seab tükeldamistehnoloogiale suuremaid nõudmisi. Suuremad kiivid vajavad lõiketeede täpsemat juhtimist, eriti suure tihedusega vooluringipiirkondades, kus isegi väikesed kõrvalekalded võivad põhjustada mitme kiibi defekti. Lisaks hõlmavad suuremad kiibid rohkem lõikejooni ja keerukamaid protsessietappe, mis nõuab tükeldamistehnoloogiate täpsuse, järjepidevuse ja tõhususe edasist täiustamist, et nendele väljakutsetele vastata.
1.3 Vahvli tükeldamise protsess
Vahvlite tükeldamisprotsess hõlmab kõiki samme alates ettevalmistusfaasist kuni lõpliku kvaliteedikontrollini, kusjuures iga etapp on tükeldatud kiipide kvaliteedi ja toimivuse tagamiseks kriitilise tähtsusega. Allpool on iga etapi üksikasjalik selgitus.
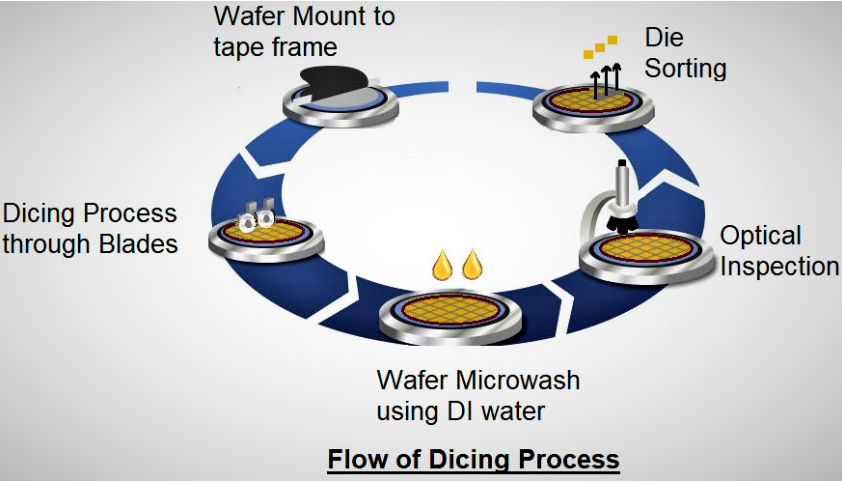
Faas | Üksikasjalik kirjeldus |
Ettevalmistusfaas | -Vahvlite puhastamineKasutage lisandite, osakeste ja saasteainete eemaldamiseks, tagades puhta pinna, kõrge puhtusastmega vett ja spetsiaalseid puhastusvahendeid koos ultraheli või mehaanilise puhastusega. -Täpne positsioneerimineKasutage ülitäpseid seadmeid, et tagada vahvli täpne jagamine kavandatud lõiketeedel. -Vahvli fikseerimineKinnitage vahvel lindiraamile, et säilitada lõikamise ajal stabiilsus, vältides vibratsioonist või liikumisest tulenevaid kahjustusi. |
Lõikamisfaas | -Tera tükeldamineKasutage füüsiliseks lõikamiseks kiirelt pöörlevaid teemantkattega lõiketerasid, mis sobivad ränipõhistele materjalidele ja on kulutõhusad. -LaserlõikusKasutage kontaktivabaks lõikamiseks suure energiaga laserkiiri, mis sobib ideaalselt habraste või suure kõvadusega materjalide, näiteks galliumnitriidi jaoks, pakkudes suuremat täpsust ja väiksemat materjalikadu. -Uued tehnoloogiadLaser- ja plasmalõikustehnoloogiate kasutuselevõtt, et veelgi parandada efektiivsust ja täpsust, minimeerides samal ajal kuumusest mõjutatud tsoone. |
Puhastusfaas | - Lõikamisel tekkivate jääkide ja tolmu eemaldamiseks kasutage deioniseeritud vett (DI vett) ja spetsiaalseid puhastusvahendeid koos ultraheli- või pihustuspuhastusega, et vältida jääkide mõju järgnevatele protsessidele või kiibi elektrilisele jõudlusele. - Kõrge puhtusastmega deioniseeritud vesi hoiab ära uute saasteainete sissetoomise, tagades puhta vahvlikeskkonna. |
Kontrolli etapp | -Optiline kontrollKasutage optilisi tuvastussüsteeme koos tehisintellekti algoritmidega defektide kiireks tuvastamiseks, tagades pragude või mõrade puudumise tükeldatud kiipides, parandades kontrolli efektiivsust ja vähendades inimlikke vigu. -Mõõtmete mõõtmineVeenduge, et kiibi mõõtmed vastavad konstruktsiooni spetsifikatsioonidele. -Elektrilise jõudluse testimineTagada kriitiliste kiipide elektrilise jõudluse vastavus standarditele, mis garanteerib töökindluse järgnevates rakendustes. |
Sorteerimisfaas | - Kasutage robotkäsi või vaakum-iminappa, et eraldada kvalifitseeritud kiibid lindiraamilt ja sorteerida need automaatselt jõudluse alusel, tagades tootmise efektiivsuse ja paindlikkuse ning parandades täpsust. |
Kiipide lõikamise protsess hõlmab kiipide puhastamist, positsioneerimist, lõikamist, puhastamist, kontrollimist ja sorteerimist, kusjuures iga samm on kriitilise tähtsusega. Tänu automatiseerimise, laserlõikuse ja tehisintellektil põhinevate kontrollitehnoloogiate arengule suudavad tänapäevased kiipide lõikamise süsteemid saavutada suurema täpsuse, kiiruse ja väiksema materjalikadu. Tulevikus asendavad uued lõiketehnoloogiad, nagu laser ja plasma, järk-järgult traditsioonilise teraga lõikamise, et rahuldada üha keerukamate kiipide disainide vajadusi, soodustades veelgi pooljuhtide tootmisprotsesside arengut.
Vahvlite lõikamise tehnoloogia ja selle põhimõtted
Pilt illustreerib kolme levinud vahvlilõikamise tehnoloogiat:Tera tükeldamine,LaserlõikusjaPlasma tükeldamineAllpool on esitatud nende kolme tehnika üksikasjalik analüüs ja täiendav selgitus:
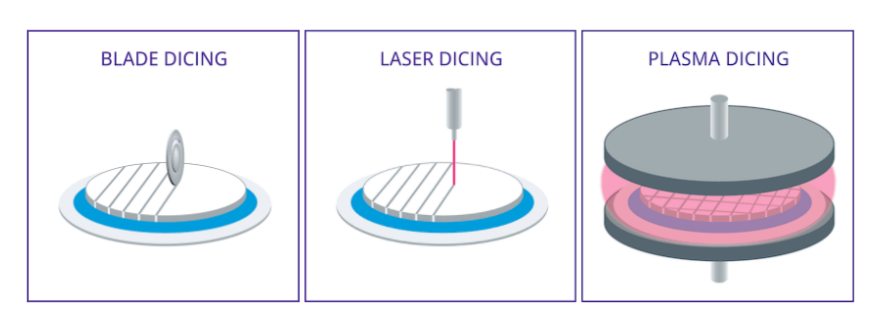
Pooljuhtide tootmises on kiipide lõikamine ülioluline samm, mis nõuab kiibi paksusele tugineva sobiva lõikemeetodi valimist. Esimene samm on kiibi paksuse määramine. Kui kiibi paksus ületab 100 mikronit, saab lõikemeetodiks valida teraga tükeldamise. Kui teraga tükeldamine ei sobi, saab kasutada murdumis- ja tükeldamismeetodit, mis hõlmab nii joonlõikamist kui ka teraga tükeldamise tehnikaid.
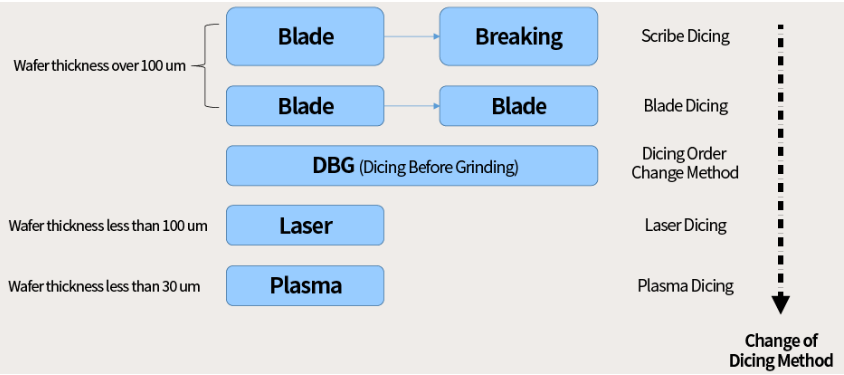
Kui vahvli paksus on 30–100 mikronit, on soovitatav kasutada DBG (Dice Before Grinding ehk kuubikuteks lõikamine enne jahvatamist) meetodit. Parima tulemuse saavutamiseks saab valida kriipslõikuse, teraga kuubikuteks lõikamise või lõikejärjestuse kohandamise vastavalt vajadusele.
Üliõhukeste vahvlite puhul, mille paksus on alla 30 mikroni, on eelistatud meetod laserlõikus, kuna see võimaldab õhukesi vahvleid täpselt lõigata ilma liigset kahju tekitamata. Kui laserlõikus ei suuda erinõudeid täita, saab alternatiivina kasutada plasmalõikust. See vooskeem annab selge otsustusprotsessi, et tagada sobivaima vahvlilõikamistehnoloogia valimine erinevate paksusetingimuste korral.
2.1 Mehaaniline lõiketehnoloogia
Mehaaniline lõiketehnoloogia on traditsiooniline meetod vahvlite tükeldamisel. Põhiprintsiip on kasutada kiirelt pöörlevat teemantlihvketast lõikevahendina vahvli viilutamiseks. Peamiste seadmete hulka kuulub õhklaagriga spindl, mis paneb teemantlihvketta tööriista suurel kiirusel käima, et teostada täpset lõikamist või soonte tegemist mööda etteantud lõiketeed. Seda tehnoloogiat kasutatakse tööstuses laialdaselt tänu oma madalale hinnale, kõrgele tõhususele ja laiale rakendatavusele.
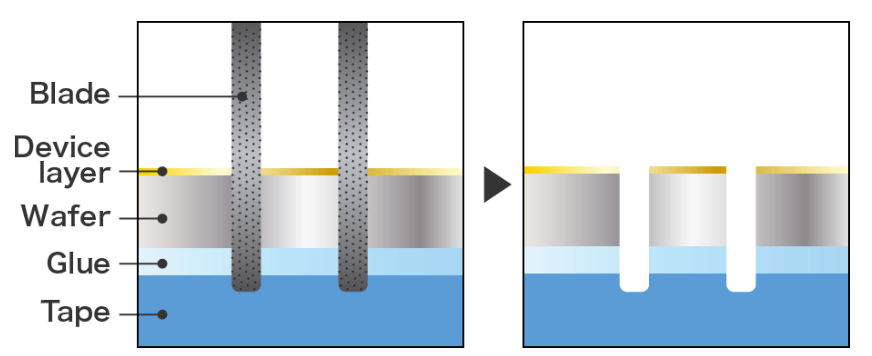
Eelised
Teemantlihvketaste kõrge kõvadus ja kulumiskindlus võimaldavad mehaanilisel lõiketehnoloogial kohaneda erinevate kiibimaterjalide lõikevajadustega, olgu need siis traditsioonilised ränipõhised materjalid või uuemad liitpooljuhid. Selle tööpõhimõte on lihtne ja tehnilised nõuded on suhteliselt madalad, mis soodustab selle populaarsust masstootmises. Lisaks on mehaanilisel lõikel võrreldes teiste lõikemeetoditega, näiteks laserlõikusega, paremini kontrollitavad kulud, mistõttu sobib see suuremahuliseks tootmiseks.
Piirangud
Vaatamata arvukatele eelistele on mehaanilisel lõiketehnoloogial ka piirangud. Esiteks on tööriista ja kiibi vahelise füüsilise kontakti tõttu lõiketäpsus suhteliselt piiratud, mis sageli viib mõõtmete kõrvalekalleteni, mis võivad mõjutada järgneva kiibi pakendamise ja testimise täpsust. Teiseks võivad mehaanilise lõikeprotsessi käigus kergesti tekkida defektid, näiteks mõrad ja praod, mis mitte ainult ei mõjuta saagikust, vaid võib negatiivselt mõjutada ka kiipide töökindlust ja eluiga. Mehaanilisest pingest tingitud kahjustused on eriti kahjulikud suure tihedusega kiipide tootmisel, eriti habraste materjalide lõikamisel, kus need probleemid on silmatorkavamad.
Tehnoloogilised täiustused
Nende piirangute ületamiseks optimeerivad teadlased pidevalt mehaanilist lõikeprotsessi. Peamised täiustused hõlmavad lihvketaste konstruktsiooni ja materjalivaliku täiustamist, et parandada lõiketäpsust ja vastupidavust. Lisaks on lõikeseadmete konstruktsioonilise disaini ja juhtimissüsteemide optimeerimine veelgi parandanud lõikeprotsessi stabiilsust ja automatiseerimist. Need edusammud vähendavad inimeste tegevusest tingitud vigu ja parandavad lõigete järjepidevust. Täiustatud kontrolli- ja kvaliteedikontrolli tehnoloogiate kasutuselevõtt lõikeprotsessi anomaaliate reaalajas jälgimiseks on samuti oluliselt parandanud lõikekindlust ja saagikust.
Tulevane areng ja uued tehnoloogiad
Kuigi mehaanilisel lõiketehnoloogial on pooljuhtide lõikamisel endiselt oluline positsioon, arenevad uued lõiketehnoloogiad kiiresti koos pooljuhtide protsesside arenemisega. Näiteks termilise laserlõikuse tehnoloogia rakendamine pakub uusi lahendusi mehaanilise lõikamise täpsuse ja defektide probleemidele. See kontaktivaba lõikemeetod vähendab pooljuhtidele avalduvat füüsilist pinget, vähendades oluliselt mõranemise ja pragunemise esinemissagedust, eriti hapramate materjalide lõikamisel. Tulevikus annab mehaanilise lõiketehnoloogia integreerimine uute lõiketehnikatega pooljuhtide tootmisele rohkem võimalusi ja paindlikkust, parandades veelgi tootmise efektiivsust ja kiibi kvaliteeti.
Kokkuvõtteks võib öelda, et kuigi mehaanilisel lõiketehnoloogial on teatud puudusi, võimaldab pidev tehnoloogiline täiustamine ja selle integreerimine uute lõiketehnikatega sellel siiski olulist rolli pooljuhtide tootmises mängida ja säilitada oma konkurentsivõime tulevastes protsessides.
2.2 Laserlõikustehnoloogia
Laserlõikustehnoloogia kui uus meetod kiipide lõikamisel on pooljuhtide tööstuses järk-järgult laialdast tähelepanu pälvinud tänu oma suurele täpsusele, mehaaniliste kontaktkahjustuste puudumisele ja kiirele lõikamisvõimele. See tehnoloogia kasutab laserkiire suurt energiatihedust ja fokuseerimisvõimet, et luua kiibimaterjali pinnale väike kuumusest mõjutatud tsoon. Kui laserkiir kiibile rakendatakse, põhjustab tekkiv termiline pinge materjali purunemise määratud kohas, saavutades täpse lõikamise.
Laserlõikustehnoloogia eelised
• Suur täpsusLaserkiire täpne positsioneerimisvõime võimaldab mikroni- või isegi nanomeetritasemel lõiketäpsust, mis vastab tänapäevase ülitäpse ja suure tihedusega integraallülituste tootmise nõuetele.
• Mehaaniline kontakt puudubLaserlõikus väldib füüsilist kontakti vahvliga, ennetades mehaanilise lõikamise käigus esinevaid levinud probleeme, nagu mõranemine ja pragunemine, parandades oluliselt kiipide saagikust ja töökindlust.
• Kiire lõikekiirusLaserlõikuse suur kiirus aitab kaasa tootmise efektiivsuse suurenemisele, muutes selle eriti sobivaks suuremahuliste ja kiirete tootmisstsenaariumide jaoks.
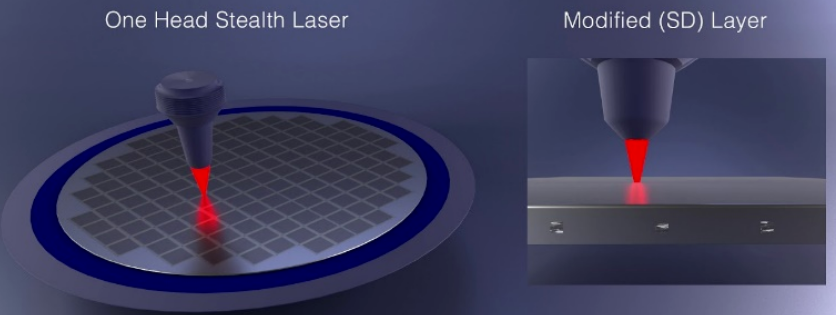
Väljakutsed
• Kõrge seadmete hindLaserlõikusseadmete alginvesteering on suur, mis tekitab majanduslikku survet, eriti väikestele ja keskmise suurusega tootmisettevõtetele.
• Kompleksne protsesside juhtimineLaserlõikus nõuab mitme parameetri, sealhulgas energiatiheduse, fookusasendi ja lõikekiiruse täpset juhtimist, mis muudab protsessi keerukaks.
• Kuumusest mõjutatud tsooni probleemidKuigi laserlõikuse kontaktivaba olemus vähendab mehaanilisi kahjustusi, võib kuummõjutsoonist (HAZ) tingitud termiline pinge negatiivselt mõjutada vahvlimaterjali omadusi. Selle mõju minimeerimiseks on vaja protsessi edasist optimeerimist.
Tehnoloogilise täiustamise suunad
Nende probleemide lahendamiseks keskenduvad teadlased seadmete kulude vähendamisele, lõikamise efektiivsuse parandamisele ja protsessivoo optimeerimisele.
• Tõhusad laserid ja optilised süsteemidTõhusamate laserite ja täiustatud optiliste süsteemide arendamise abil on võimalik vähendada seadmete kulusid, suurendades samal ajal lõiketäpsust ja -kiirust.
• Protsessi parameetrite optimeerimineKuummõjutsooni vähendamise ja seeläbi lõikekvaliteeti parandavate protsesside täiustamiseks viiakse läbi põhjalikke uuringuid laserite ja kiibimaterjalide vastastikmõju kohta.
• Intelligentsed juhtimissüsteemidIntelligentsete juhtimistehnoloogiate arendamise eesmärk on laserlõikusprotsessi automatiseerimine ja optimeerimine, parandades selle stabiilsust ja järjepidevust.
Laserlõikustehnoloogia on eriti efektiivne üliõhukeste vahvlite ja ülitäpse lõikamise stsenaariumides. Kuna vahvlite suurused ja vooluringide tihedus suurenevad, on traditsioonilistel mehaanilistel lõikemeetoditel raskusi tänapäevase pooljuhtide tootmise ülitäpsete ja ülitõhusate nõuete täitmisega. Tänu oma ainulaadsetele eelistele on laserlõikus muutumas eelistatud lahenduseks nendes valdkondades.
Kuigi laserlõikustehnoloogia seisab endiselt silmitsi selliste väljakutsetega nagu seadmete kõrge hind ja protsessi keerukus, muudavad selle ainulaadsed eelised suure täpsuse ja kontaktivaba kahjustuste osas selle pooljuhtide tootmise oluliseks arengusuunaks. Kuna lasertehnoloogia ja intelligentsed juhtimissüsteemid arenevad pidevalt, eeldatakse, et laserlõikus parandab veelgi kiipide lõikamise efektiivsust ja kvaliteeti, soodustades pooljuhtide tööstuse pidevat arengut.
2.3 Plasmalõikuse tehnoloogia
Plasmalõikustehnoloogia kui uus kiipide tükeldamismeetod on viimastel aastatel pälvinud märkimisväärset tähelepanu. See tehnoloogia kasutab kiipide täpseks lõikamiseks suure energiaga plasmakiiri, kontrollides plasmakiire energiat, kiirust ja lõiketeed, saavutades optimaalsed lõiketulemused.
Tööpõhimõte ja eelised
Plasmalõikuse protsess tugineb seadme tekitatud kõrge temperatuuriga ja suure energiaga plasmakiirele. See kiir suudab kiibimaterjali väga lühikese aja jooksul sulamis- või aurustumistemperatuurini kuumutada, võimaldades kiiret lõikamist. Võrreldes traditsioonilise mehaanilise või laserlõikusega on plasmalõikus kiirem ja tekitab väiksema kuumusest mõjutatud tsooni, vähendades tõhusalt pragude ja kahjustuste tekkimist lõikamise ajal.
Praktilistes rakendustes on plasmalõikustehnoloogia eriti osav keeruka kujuga vahvlite käsitsemisel. Selle suure energiaga ja reguleeritav plasmakiir suudab hõlpsalt ja täpselt lõigata ebakorrapärase kujuga vahvleid. Seetõttu on sellel tehnoloogial mikroelektroonika tootmises, eriti tipptasemel kiipide kohandatud ja väikeste partiide tootmisel, suur potentsiaali laialdaseks kasutamiseks.
Väljakutsed ja piirangud
Vaatamata plasmalõikustehnoloogia paljudele eelistele on sellel ka mõningaid väljakutseid.
• Keerukas protsessPlasmalõikusprotsess on keerukas ja nõuab ülitäpseid seadmeid ning kogenud operaatoreid, et tagadatäpsus ja stabiilsus lõikamisel.
• Keskkonnakontroll ja -ohutusPlasmakiire kõrge temperatuur ja kõrge energia nõuab rangeid keskkonnakontrolli ja ohutusmeetmeid, mis suurendab rakendamise keerukust ja kulusid.
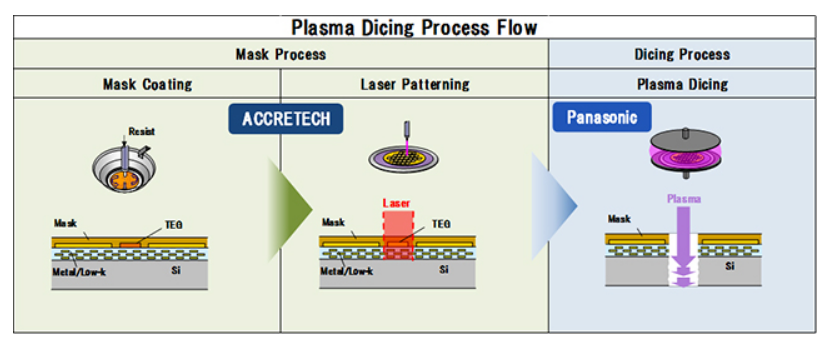
Tulevased arengusuunad
Tehnoloogia arenguga loodetakse plasmalõikusega seotud väljakutseid järk-järgult ületada. Nutikamate ja stabiilsemate lõikeseadmete arendamise abil saab vähendada sõltuvust käsitsi toimingutest, parandades seeläbi tootmise efektiivsust. Samal ajal aitab protsessiparameetrite ja lõikekeskkonna optimeerimine vähendada ohutusriske ja tegevuskulusid.
Pooljuhtide tööstuses on kiipide lõikamise ja tükeldamise tehnoloogia innovatsioonid tööstuse arengu edendamiseks üliolulised. Plasmalõikustehnoloogia on oma suure täpsuse, efektiivsuse ja keerukate kiipide kujude käsitlemise võimega selles valdkonnas esile kerkinud olulise uue tegijana. Kuigi mõned väljakutsed on endiselt lahendatud, lahendatakse need probleemid järk-järgult jätkuva tehnoloogilise innovatsiooni abil, mis toob pooljuhtide tootmisele rohkem võimalusi.
Plasmalõikustehnoloogia rakendusväljavaated on tohutud ja eeldatavasti mängib see tulevikus pooljuhtide tootmises veelgi olulisemat rolli. Pideva tehnoloogilise innovatsiooni ja optimeerimise kaudu plasmalõikus mitte ainult ei lahenda olemasolevaid probleeme, vaid saab ka pooljuhtide tööstuse kasvu võimsaks edasiviijaks.
2.4 Lõikekvaliteet ja seda mõjutavad tegurid
Vahvli lõikamise kvaliteet on kriitilise tähtsusega järgneva kiibi pakendamise, testimise ning lõpptoote üldise jõudluse ja töökindluse jaoks. Lõikamise ajal esinevate levinud probleemide hulka kuuluvad praod, mõrad ja lõikehälbed. Neid probleeme mõjutavad mitmed tegurid koos.
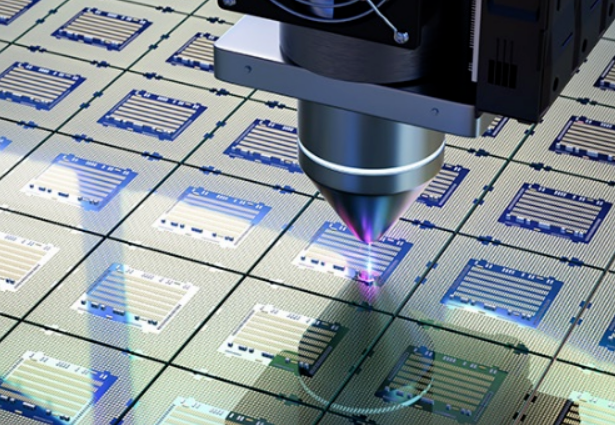
Kategooria | Sisu | Mõju |
Protsessi parameetrid | Lõikekiirus, etteandekiirus ja lõikesügavus mõjutavad otseselt lõikeprotsessi stabiilsust ja täpsust. Valed sätted võivad põhjustada pingekontsentratsiooni ja liigset kuumusest mõjutatud tsooni, mille tulemuseks on praod ja mõrad. Parameetrite sobiv reguleerimine vastavalt kiibi materjalile, paksusele ja lõikenõuetele on soovitud lõiketulemuste saavutamise võti. | Õiged protsessiparameetrid tagavad täpse lõikamise ja vähendavad defektide, näiteks pragude ja mõrade tekkimise ohtu. |
Seadmed ja materjalitegurid | -Tera kvaliteetTera materjal, kõvadus ja kulumiskindlus mõjutavad lõikeprotsessi sujuvust ja lõikepinna tasasust. Halva kvaliteediga terad suurendavad hõõrdumist ja termilist pinget, mis võib viia pragude või mõranemiseni. Õige teramaterjali valimine on ülioluline. -Jahutusvedeliku jõudlusJahutusvedelikud aitavad vähendada lõiketemperatuuri, minimeerida hõõrdumist ja eemaldada prahti. Ebatõhus jahutusvedelik võib põhjustada kõrgeid temperatuure ja prahi kogunemist, mis mõjutab lõikekvaliteeti ja -tõhusust. Tõhusate ja keskkonnasõbralike jahutusvedelike valimine on ülioluline. | Tera kvaliteet mõjutab lõike täpsust ja sujuvust. Ebatõhus jahutusvedelik võib põhjustada halba lõikekvaliteeti ja -tõhusust, mis rõhutab optimaalse jahutusvedeliku kasutamise vajadust. |
Protsessi kontroll ja kvaliteedikontroll | -Protsessi kontrollLõikeparameetrite reaalajas jälgimine ja reguleerimine lõikeprotsessi stabiilsuse ja järjepidevuse tagamiseks. -KvaliteedikontrollLõikamisjärgsed välimuse kontrollid, mõõtmete mõõtmised ja elektrilise jõudluse testid aitavad kvaliteediprobleeme kiiresti tuvastada ja lahendada, parandades lõiketäpsust ja -järjepidevust. | Nõuetekohane protsessikontroll ja kvaliteedikontroll aitavad tagada järjepidevaid ja kvaliteetseid lõiketulemusi ning võimalike probleemide varajase avastamise. |

Lõikekvaliteedi parandamine
Lõikekvaliteedi parandamine nõuab terviklikku lähenemisviisi, mis võtab arvesse protsessi parameetreid, seadmete ja materjalide valikut, protsessi juhtimist ja kontrolli. Lõiketehnoloogiate pideva täiustamise ja protsessimeetodite optimeerimise abil saab veelgi parandada kiipide lõikamise täpsust ja stabiilsust, pakkudes pooljuhtide tootmistööstusele usaldusväärsemat tehnilist tuge.
#03 Lõikamisjärgne käitlemine ja testimine
3.1 Puhastamine ja kuivatamine
Kiibi lõikamisele järgnevad puhastamise ja kuivatamise etapid on kriitilise tähtsusega kiibi kvaliteedi ja järgnevate protsesside sujuva kulgemise tagamiseks. Selles etapis on oluline ränijäägid, jahutusvedeliku jäägid ja muud lõikamise ajal tekkinud saasteained põhjalikult eemaldada. Sama oluline on tagada, et kiibid puhastamise käigus ei kahjustuks, ja pärast kuivatamist veenduda, et kiibi pinnale ei jääks niiskust, et vältida selliseid probleeme nagu korrosioon või elektrostaatiline tühjenemine.
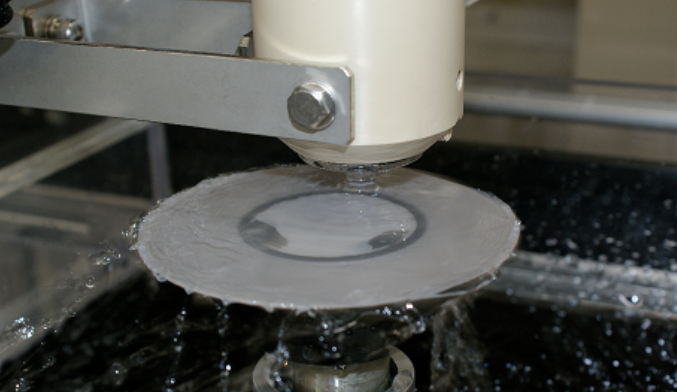
Lõikamisjärgne käitlemine: puhastamis- ja kuivatamisprotsess
Protsessi samm | Sisu | Mõju |
Puhastusprotsess | -MeetodPuhastamiseks kasutage spetsiaalseid puhastusvahendeid ja puhast vett ning kombineerige neid ultraheli või mehaanilise harjamise tehnikaga. | Tagab saasteainete põhjaliku eemaldamise ja hoiab ära laastude kahjustumise puhastamise ajal. |
-Puhastusvahendi valikValige kiibi materjali ja saasteaine tüübi põhjal, et tagada tõhus puhastamine kiipi kahjustamata. | Õige puhastusvahendi valik on tõhusa puhastamise ja kiipide kaitsmise võti. | |
-Parameetrite kontroll: Kontrollige rangelt puhastustemperatuuri, -aega ja puhastuslahuse kontsentratsiooni, et vältida ebaõigest puhastamisest tingitud kvaliteediprobleeme. | Kontrollid aitavad vältida vahvli kahjustamist või saasteainete mahajätmist, tagades ühtlase kvaliteedi. | |
Kuivamisprotsess | -Traditsioonilised meetodidLooduslik õhukuivatus ja kuuma õhuga kuivatus, millel on madal efektiivsus ja mis võivad põhjustada staatilise elektri kogunemist. | Võib põhjustada aeglasemat kuivamisaega ja potentsiaalseid staatilise elektri probleeme. |
-Kaasaegsed tehnoloogiadKasutage täiustatud tehnoloogiaid, nagu vaakumkuivatamine ja infrapunakuivatamine, et tagada kiipide kiire kuivamine ja vältida kahjulikke mõjusid. | Kiirem ja tõhusam kuivamisprotsess, mis vähendab staatilise elektri või niiskusprobleemide ohtu. | |
Seadmete valik ja hooldus | -Varustuse valikSuure jõudlusega puhastus- ja kuivatusmasinad parandavad töötlemise efektiivsust ja kontrollivad võimalikke probleeme käitlemise ajal. | Kvaliteetsed masinad tagavad parema töötlemise ja vähendavad vigade tõenäosust puhastamise ja kuivatamise ajal. |
-Seadmete hooldusSeadmete regulaarne kontroll ja hooldus tagavad nende optimaalse töökorras püsimise, garanteerides kiibi kvaliteedi. | Nõuetekohane hooldus hoiab ära seadmete rikkeid, tagades usaldusväärse ja kvaliteetse töötlemise. |
Lõikamisjärgne puhastamine ja kuivatamine
Kiipide lõikamisele järgnevad puhastamis- ja kuivatamisetapid on keerulised ja õrnad protsessid, mis nõuavad lõpliku töötlemistulemuse tagamiseks mitme teguri hoolikat kaalumist. Teaduslike meetodite ja rangete protseduuride abil on võimalik tagada, et iga kiip siseneb järgmistesse pakkimis- ja testimisetappidesse optimaalses seisukorras.
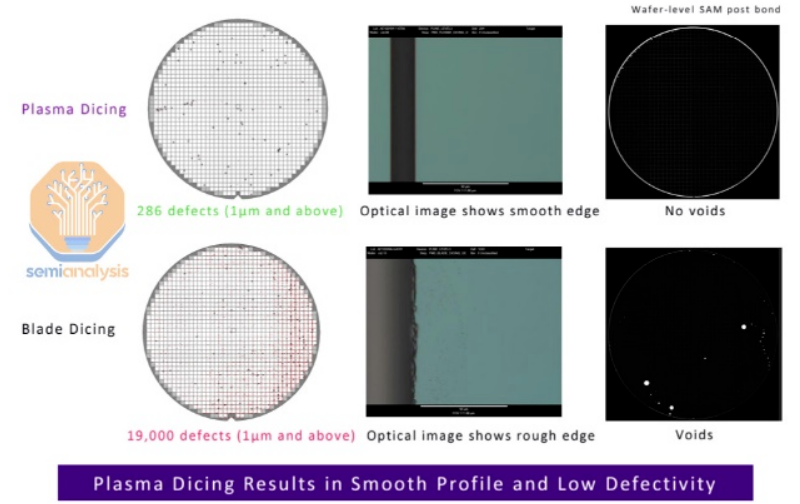
Lõikamisjärgne kontroll ja testimine
Samm | Sisu | Mõju |
Kontrolli samm | 1.Visuaalne kontrollKasutage visuaalseid või automatiseeritud kontrollseadmeid, et kontrollida kiibi pinnal nähtavaid defekte, nagu praod, mõrad või saastumine. Tuvastage kiiresti füüsiliselt kahjustatud kiibid, et vältida raiskamist. | Aitab defektseid kiipe protsessi alguses tuvastada ja kõrvaldada, vähendades materjalikadu. |
2.Suuruse mõõtmineKasutage täppismõõteseadmeid kiibi mõõtmete täpseks mõõtmiseks, tagades lõikesuuruse vastavuse projekteerimisspetsifikatsioonidele ja vältides jõudlusprobleeme või pakkimisraskusi. | Tagab, et kiibid jäävad nõutavate suuruste piiridesse, vältides jõudluse halvenemist või montaažiprobleeme. | |
3.Elektrilise jõudluse testimineHinnake olulisi elektrilisi parameetreid, nagu takistus, mahtuvus ja induktiivsus, et tuvastada mittevastavad kiibid ja tagada, et järgmisse etappi jõuaksid ainult jõudlusega kvalifitseeritud kiibid. | Tagab, et protsessis liiguvad edasi ainult funktsionaalsed ja jõudlustestitud kiibid, vähendades rikkeohtu hilisemates etappides. | |
Testimisetapp | 1.Funktsionaalne testimineVeenduge, et kiibi põhifunktsioonid toimivad ettenähtud viisil, tuvastades ja kõrvaldades funktsionaalsete kõrvalekalletega kiibid. | Tagab, et kiibid vastavad enne hilisematesse etappidesse liikumist põhilistele töönõuetele. |
2.Usaldusväärsuse testimineHinnake kiibi jõudluse stabiilsust pikaajalisel kasutamisel või karmides keskkondades, mis tavaliselt hõlmab kõrgel temperatuuril vananemist, madalal temperatuuril testimist ja niiskustestimist reaalsete äärmuslike tingimuste simuleerimiseks. | Tagab kiipide usaldusväärse toimimise erinevates keskkonnatingimustes, parandades toote pikaealisust ja stabiilsust. | |
3.Ühilduvuse testimineVeenduge, et kiip töötab teiste komponentide või süsteemidega korralikult, veendudes, et ühildumatusest tulenevaid vigu ega jõudluse halvenemist ei esine. | Tagab sujuva töö reaalsetes rakendustes, ennetades ühilduvusprobleeme. |
3.3 Pakendamine ja ladustamine
Pärast kiipide lõikamist on kiibid pooljuhtide tootmisprotsessi oluline väljund ning nende pakendamise ja ladustamise etapid on sama olulised. Nõuetekohased pakendamise ja ladustamise meetmed on olulised mitte ainult kiipide ohutuse ja stabiilsuse tagamiseks transportimise ja ladustamise ajal, vaid ka tugeva toe pakkumiseks järgnevatel tootmise, testimise ja pakendamise etappidel.
Kontrolli ja testimise etappide kokkuvõte:
Kiipide kontrolli- ja testimisetapid pärast kiipide lõikamist hõlmavad mitmesuguseid aspekte, sealhulgas visuaalset kontrolli, suuruse mõõtmist, elektrilise jõudluse testimist, funktsionaalset testimist, töökindluse testimist ja ühilduvuse testimist. Need etapid on omavahel seotud ja üksteist täiendavad, moodustades kindla barjääri toote kvaliteedi ja töökindluse tagamiseks. Rangete kontrolli- ja testimisprotseduuride abil saab potentsiaalseid probleeme kiiresti tuvastada ja lahendada, tagades, et lõpptoode vastab klientide nõuetele ja ootustele.
Aspekt | Sisu |
Pakkimismeetmed | 1.AntistaatilinePakkematerjalidel peaksid olema suurepärased antistaatilised omadused, et vältida staatilise elektri tekitatud kahju seadmetele või nende jõudluse mõjutamist. |
2.NiiskuskindelPakkematerjalidel peaks olema hea niiskuskindlus, et vältida niiskuse põhjustatud korrosiooni ja elektrilise jõudluse halvenemist. | |
3.LöögikindelPakkematerjalid peaksid transportimise ajal pakkuma tõhusat löökide neeldumist, et kaitsta kiipe vibratsiooni ja löökide eest. | |
Salvestuskeskkond | 1.Niiskuse kontrollNiiskusesisaldust tuleb rangelt reguleerida sobivas vahemikus, et vältida liigsest niiskusest tingitud niiskuse imendumist ja korrosiooni või madalast niiskusest tingitud staatilisi probleeme. |
2.PuhtusHoidke laastude saastumise vältimiseks tolmu ja lisanditega puhast hoiukeskkonda. | |
3.Temperatuuri kontroll: Määrake mõistlik temperatuurivahemik ja hoidke temperatuuri stabiilsust, et vältida kiirenenud vananemist madalate temperatuuride põhjustatud liigse kuumuse või kondensatsiooniprobleemide tõttu. | |
Regulaarne kontroll | Kontrollige ja hinnake ladustatud kiipe regulaarselt visuaalse kontrolli, suuruse mõõtmise ja elektrilise jõudluse testide abil, et õigeaegselt tuvastada ja lahendada võimalikke probleeme. Planeerige kiipide kasutamist, lähtudes ladustamisajast ja -tingimustest, et tagada nende optimaalne seisukord. |
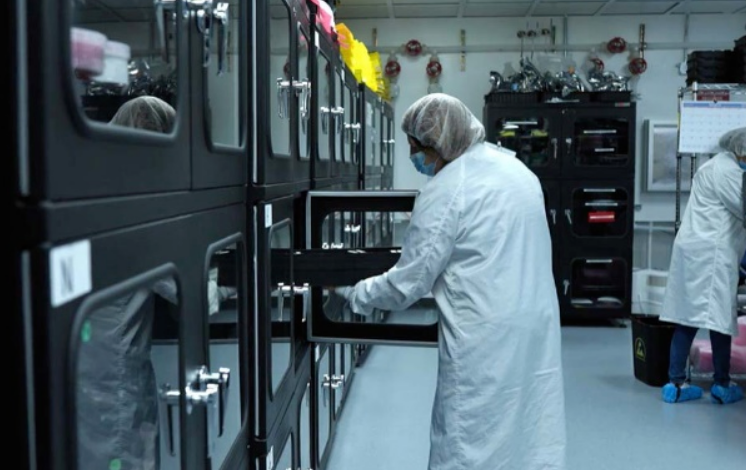
Mikropragude ja kahjustuste probleem pooljuhtide tootmisel on märkimisväärne väljakutse. Lõikepinge on selle nähtuse peamine põhjus, kuna see tekitab vahvli pinnale pisikesi pragusid ja kahjustusi, mis suurendab tootmiskulusid ja langetab toote kvaliteeti.
Selle probleemi lahendamiseks on oluline minimeerida lõikepinget ning rakendada optimeeritud lõiketehnikaid, tööriistu ja tingimusi. Selliste tegurite nagu tera materjal, lõikekiirus, rõhk ja jahutusmeetodid hoolikas arvestamine aitab vähendada mikropragude teket ja parandada protsessi üldist saagikust. Lisaks uuritakse käimasolevate uuringutega täiustatud lõiketehnoloogiate, näiteks laserlõikuse, kohta võimalusi nende probleemide edasiseks leevendamiseks.
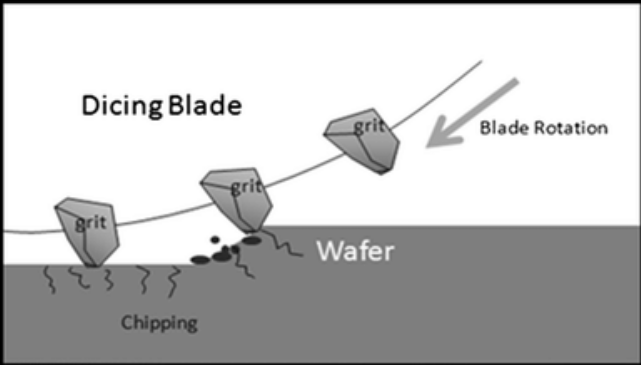
Habras materjalina on vahvlid mehaanilise, termilise või keemilise pinge all olles altid sisemistele struktuurimuutustele, mis viib mikropragude tekkeni. Kuigi need praod ei pruugi kohe märgatavad olla, võivad need tootmisprotsessi edenedes laieneda ja põhjustada tõsisemaid kahjustusi. See probleem muutub eriti problemaatiliseks järgnevates pakkimis- ja testimisetappides, kus temperatuurikõikumised ja täiendavad mehaanilised pinged võivad põhjustada nende mikropragude arenemist nähtavateks pragudeks, mis võib viia kiibi purunemiseni.
Selle riski maandamiseks on oluline lõikamisprotsessi hoolikalt kontrollida, optimeerides parameetreid, nagu lõikekiirus, rõhk ja temperatuur. Vähem agressiivsete lõikemeetodite, näiteks laserlõikuse kasutamine võib vähendada vahvli mehaanilist pinget ja minimeerida mikropragude teket. Lisaks aitab täiustatud kontrollimeetodite, näiteks infrapunaskaneerimise või röntgenpildistamise rakendamine vahvli lõikamisprotsessi ajal tuvastada neid varajases staadiumis pragusid enne, kui need põhjustavad edasist kahju.
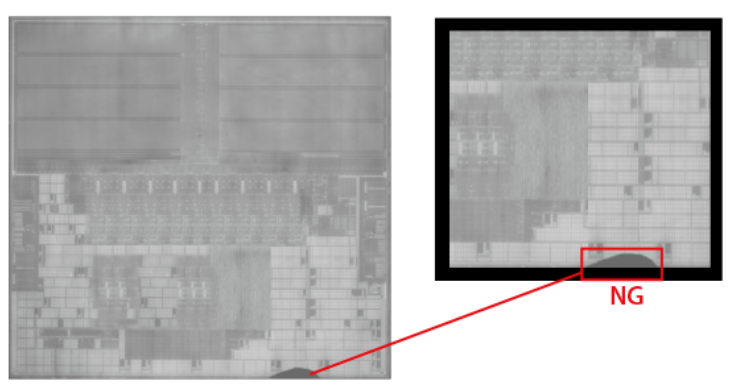
Kiibi pinna kahjustused on tükeldamisprotsessis oluline probleem, kuna need võivad otseselt mõjutada kiibi jõudlust ja töökindlust. Sellised kahjustused võivad tekkida lõikeriistade ebaõige kasutamise, valede lõikeparameetrite või kiibi enda materjalidefektide tõttu. Olenemata põhjusest võivad need kahjustused põhjustada muutusi vooluahela elektritakistuses või mahtuvuses, mis mõjutab üldist jõudlust.
Nende probleemide lahendamiseks uuritakse kahte peamist strateegiat:
1. Lõikeriistade ja parameetrite optimeerimineTeravamate terade kasutamise, lõikekiiruse reguleerimise ja lõikesügavuse muutmise abil saab lõikeprotsessi ajal tekkivat pinget minimeerida, vähendades seeläbi kahjustuste tekkimise võimalust.
2. Uute lõiketehnoloogiate uurimineTäiustatud tehnikad, nagu laserlõikus ja plasmalõikus, pakuvad paremat täpsust, vähendades samal ajal potentsiaalselt kiibile tekitatud kahjustuste taset. Neid tehnoloogiaid uuritakse, et leida viise suure lõiketäpsuse saavutamiseks, minimeerides samal ajal kiibile avaldatavat termilist ja mehaanilist pinget.
Termilise mõju ala ja selle mõju jõudlusele
Termilise lõikamise protsessides, nagu laser- ja plasmalõikus, tekitab kõrge temperatuur paratamatult kiibi pinnale termilise löögitsooni. See piirkond, kus temperatuurigradient on märkimisväärne, võib muuta materjali omadusi, mõjutades kiibi lõplikku jõudlust.
Termilise mõjuga tsooni (TAZ) mõju:
Kristallstruktuuri muutusedKõrgete temperatuuride mõjul võivad kiibimaterjali aatomid ümber paigutuda, põhjustades kristallstruktuuri moonutusi. See moonutus nõrgestab materjali, vähendades selle mehaanilist tugevust ja stabiilsust, mis omakorda suurendab kiibi rikke ohtu kasutamise ajal.
Elektriliste omaduste muutusedKõrged temperatuurid võivad muuta pooljuhtmaterjalides laengukandjate kontsentratsiooni ja liikuvust, mõjutades kiibi elektrijuhtivust ja vooluülekande efektiivsust. Need muutused võivad viia kiibi jõudluse languseni, muutes selle potentsiaalselt sihtotstarbeliseks kasutamiseks sobimatuks.
Nende mõjude leevendamiseks on temperatuuri kontrollimine lõikamise ajal, lõikeparameetrite optimeerimine ja selliste meetodite nagu jahutusdüüside või järeltöötlusmeetodite uurimine olulised strateegiad termilise mõju ulatuse vähendamiseks ja materjali terviklikkuse säilitamiseks.
Üldiselt on nii mikropraod kui ka termilise löögi tsoonid kiipide tükeldamise tehnoloogias olulised väljakutsed. Pooljuhttoodete kvaliteedi parandamiseks ja nende turukonkurentsivõime suurendamiseks on vaja jätkuvat uurimistööd koos tehnoloogiliste edusammude ja kvaliteedikontrolli meetmetega.
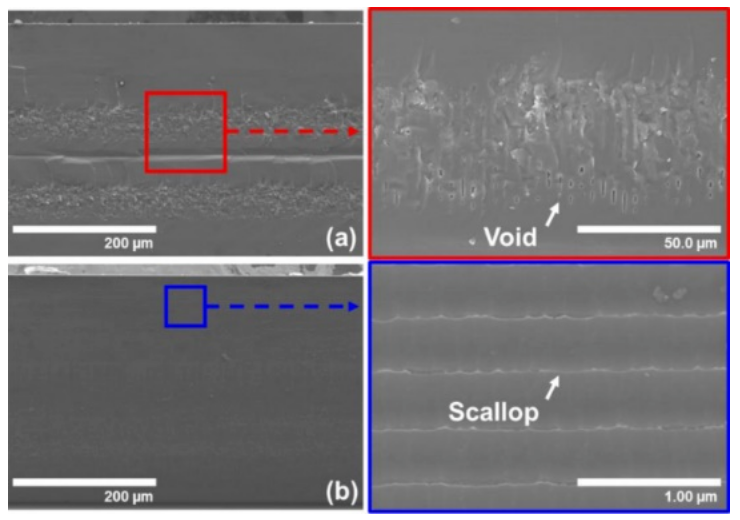
Termilise mõju tsooni kontrollimise meetmed:
Lõikeprotsessi parameetrite optimeerimineLõikekiiruse ja -võimsuse vähendamine aitab tõhusalt minimeerida termilise löögitsooni (TAZ) suurust. See aitab kontrollida lõikamisprotsessi käigus tekkivat soojushulka, mis mõjutab otseselt vahvli materjali omadusi.
Täiustatud jahutustehnoloogiadSelliste tehnoloogiate nagu vedela lämmastikuga jahutamine ja mikrofluidjahutus rakendamine võib termilise löögitsooni ulatust oluliselt piirata. Need jahutusmeetodid aitavad soojust tõhusamalt hajutada, säilitades seeläbi vahvli materjali omadused ja minimeerides termilisi kahjustusi.
Materjali valikTeadlased uurivad uusi materjale, näiteks süsiniknanotorusid ja grafeeni, millel on suurepärane soojusjuhtivus ja mehaaniline tugevus. Need materjalid võivad vähendada termilise löögi tsooni, parandades samal ajal kiipide üldist jõudlust.
Kokkuvõttes võib öelda, et kuigi termilise löögi tsoon on termilise lõikamise tehnoloogiate vältimatu tagajärg, saab seda tõhusalt kontrollida optimeeritud töötlemistehnikate ja materjalivaliku abil. Edasised uuringud keskenduvad tõenäoliselt termilise lõikamise protsesside peenhäälestamisele ja automatiseerimisele, et saavutada tõhusam ja täpsem kiipide tükeldamine.

Tasakaalu strateegia:
Vahvlite saagikuse ja tootmistõhususe vahelise optimaalse tasakaalu saavutamine on vahvlite tükeldamistehnoloogias pidev väljakutse. Tootjad peavad ratsionaalse tootmisstrateegia ja protsessiparameetrite väljatöötamiseks arvestama mitmete teguritega, nagu turunõudlus, tootmiskulud ja toote kvaliteet. Samal ajal on täiustatud lõikeseadmete kasutuselevõtt, operaatorite oskuste parandamine ja tooraine kvaliteedikontrolli tõhustamine olulised saagikuse säilitamiseks või isegi parandamiseks, suurendades samal ajal tootmise efektiivsust.
Tulevased väljakutsed ja võimalused:
Pooljuhtide tehnoloogia arenguga seisab kiipide lõikamine silmitsi uute väljakutsete ja võimalustega. Kiibi suuruste vähenemise ja integreerimise suurenemisega kasvavad märkimisväärselt nõudmised lõikamise täpsuse ja kvaliteedi osas. Samal ajal pakuvad uued tehnoloogiad uusi ideid kiipide lõikamise tehnikate arendamiseks. Tootjad peavad olema kursis turudünaamika ja tehnoloogiliste suundumustega, kohandades ja optimeerides pidevalt tootmisstrateegiaid ja protsessiparameetreid, et vastata turumuutustele ja tehnoloogilistele nõudmistele.
Kokkuvõtteks võib öelda, et turunõudluse, tootmiskulude ja tootekvaliteedi kaalutluste integreerimise ning täiustatud seadmete ja tehnoloogia kasutuselevõtu, operaatorite oskuste parandamise ja tooraine kontrolli tugevdamise abil saavad tootjad saavutada parima tasakaalu vahvlite saagikuse ja tootmistõhususe vahel vahvlite tükeldamise ajal, mis viib tõhusa ja kvaliteetse pooljuhttoodete tootmiseni.
Tulevikuväljavaated:
Kiirete tehnoloogiliste edusammudega areneb pooljuhtide tehnoloogia enneolematu kiirusega. Pooljuhtide tootmise kriitilise sammuna on kiibilõikamise tehnoloogia valmis põnevateks uuteks arenguteks. Tulevikku vaadates eeldatakse, et kiibilõikamise tehnoloogia saavutab olulisi parandusi täpsuse, efektiivsuse ja kulude osas, andes pooljuhtide tööstuse jätkuvale kasvule uut elujõudu.
Täpsuse suurendamine:
Suurema täpsuse poole püüdlemisel nihutab kiipide lõikamise tehnoloogia pidevalt olemasolevate protsesside piire. Lõikeprotsessi füüsikaliste ja keemiliste mehhanismide põhjaliku uurimise ning lõikeparameetrite täpse juhtimise abil saavutatakse peenemad lõiketulemused, et rahuldada üha keerukamaid vooluringide projekteerimisnõudeid. Lisaks parandab uute materjalide ja lõikemeetodite uurimine oluliselt saagikust ja kvaliteeti.
Tõhususe suurendamine:
Uued kiibilõikamisseadmed keskenduvad nutikale ja automatiseeritud disainile. Täiustatud juhtimissüsteemide ja algoritmide kasutuselevõtt võimaldab seadmetel lõikeparameetreid automaatselt kohandada vastavalt erinevatele materjalidele ja disaininõuetele, parandades seeläbi oluliselt tootmise efektiivsust. Tõhususe suurendamisel mängivad olulist rolli sellised uuendused nagu mitme kiibi lõikamise tehnoloogia ja terade kiire vahetuse süsteemid.
Kulude vähendamine:
Kulude vähendamine on kiipide lõikamise tehnoloogia arendamise põhisuund. Uute materjalide ja lõikemeetodite väljatöötamisel eeldatakse, et seadmete kulusid ja hoolduskulusid saab tõhusalt kontrollida. Lisaks vähendab tootmisprotsesside optimeerimine ja praagi vähendamine veelgi tootmise käigus tekkivat jäätmeid, mis viib üldiste tootmiskulude vähenemiseni.
Nutikas tootmine ja asjade internet:
Nutika tootmise ja asjade interneti (IoT) tehnoloogiate integreerimine toob kaasa murrangulisi muutusi kiipide lõikamise tehnoloogias. Seadmete omavahelise ühendatuse ja andmete jagamise kaudu saab tootmisprotsessi iga etappi reaalajas jälgida ja optimeerida. See mitte ainult ei paranda tootmise efektiivsust ja tootekvaliteeti, vaid pakub ettevõtetele ka täpsemat turuprognoosi ja otsuste tegemise tuge.
Tulevikus teeb kiipide lõikamise tehnoloogia märkimisväärseid edusamme täpsuse, efektiivsuse ja kulude osas. Need edusammud soodustavad pooljuhtide tööstuse edasist arengut ning toovad inimühiskonda rohkem tehnoloogilisi uuendusi ja mugavusi.
Postituse aeg: 19. november 2024